Mark Ferrante started laying tile in his teens, working alongside his father. “It was so rewarding to turn a shell of a space into a thing of beauty,” he says. “I still love creating that transformation.”
Mark’s father, Carmine, founded the family business, Ferrante Tile, in 1954, handing down the old-world techniques he was taught, such as laying thick beds of hand-mixed mortar to lock tile in place. He also stressed the importance of starting with a well-prepared, perfectly level surface. “My father taught me to go all out on the prep work—it takes more time, but we get it right and we don’t have problems,” says Mark, who’s been the go-to tiling contractor on more than a dozen TOH project houses.
Today, Mark works with his own son, Erik, using a mix of traditional and modern methods. On these pages, he shares tiling advice for DIYers or those hiring a pro. “Once you understand the materials and techniques, you can make sure you’re getting a quality job.”
Before You Begin: Finding the Right Base
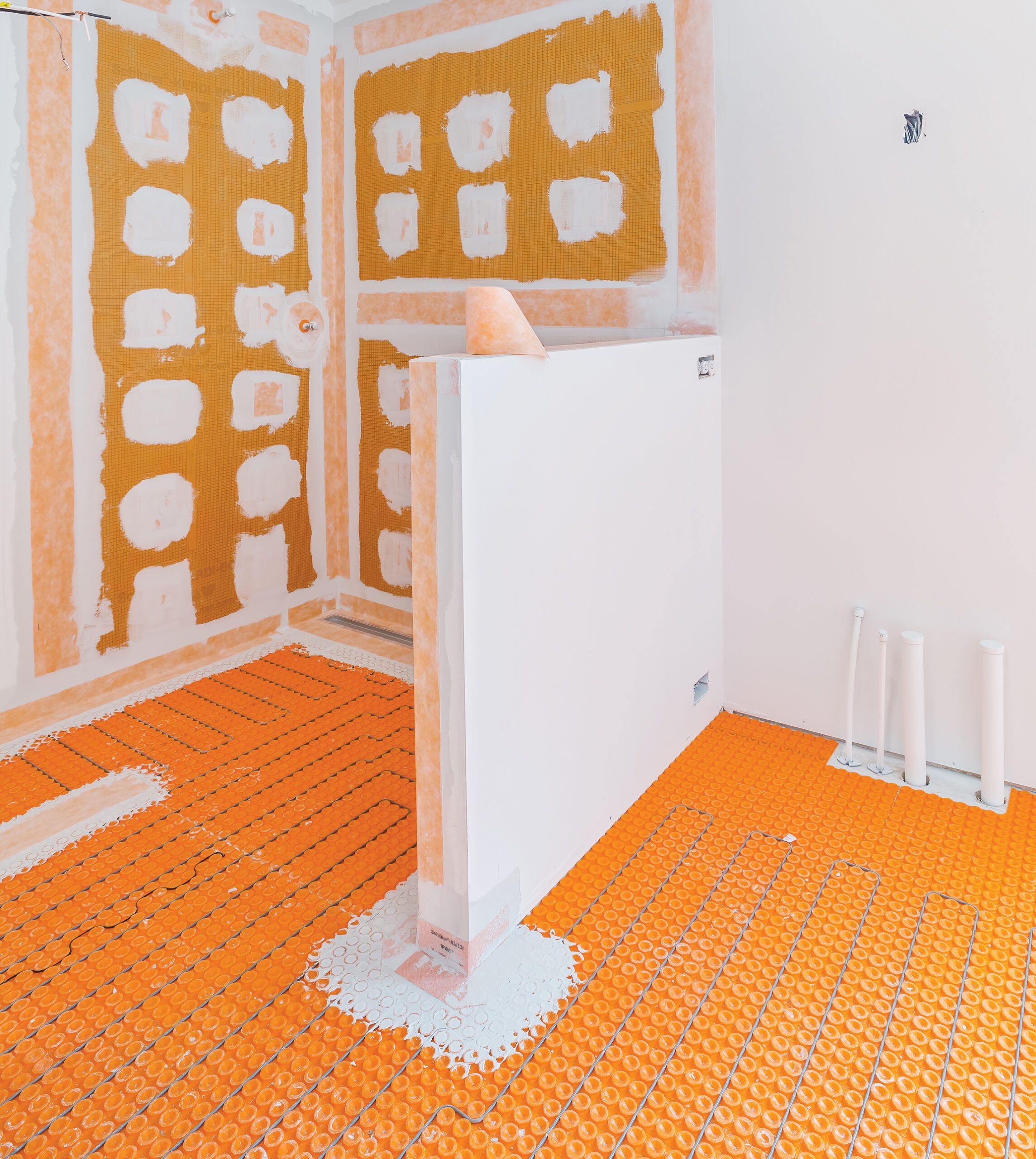
Tile needs a supportive, rigid base. If installed directly on a surface that flexes and swells, such as plywood, it can crack and crumble. Here’s how to think about underlayment options.
Mortar bed
The original tile underlayment, brought to the United States by Italian immigrants in the 1800s, is a hand-laid bed of concrete troweled in place on walls or floors—a process that requires pro-level skills.
Still considered the top-quality underlayment, and Mark’s choice when a project isn’t facing time or budget constraints, a mortar bed provides the best surface for adhering tile, can flatten out inconsistencies in the subfloor, and can be pitched to the drain for shower floors.
Cement board/fiber cement
These hard concrete panels are a dependable, easy-to-install choice for floors and walls; cement board is reinforced with fiberglass, while fiber cement has added cellulose fibers to make it easier to cut.
They’re screwed to the substrate and finished with tape and compound over joints and screw holes. They’re water resistant but not waterproof, so when using them in a wet area, Mark adds moisture protection. First, he skim-coats the cement board with latex-modified thinset; then he uses a paint roller to apply a
Foam board
Lightweight and easy to cut with a blade, foam board is expensive, but it’s also waterproof and is a vapor barrier when sealed with companion products made by the same manufacturer.
Self-leveling underlayment
This mix-it-yourself compound of portland cement and polymers is poured and spread over the subfloor with a tined rake, then left to find level and cure into a hard surface. Prep is extensive and includes closing up even tiny holes or gaps in the subfloor so the material doesn’t pour through; creating an expansion gap around the perimeter, typically using sill seal foam; applying a primer; and stapling down metal lath.
Glass-mat gypsum
This water-resistant drywall with a fiberglass-mat surface is lightweight and easy to install but can be used only on walls.
Uncoupling membrane
Good for floors and walls, this is a dimpled polyethylene or polypropylene layer that prevents shifting in the structure underneath from affecting the tile above. At 1/8 inch thick, it adds minimal height at floor transitions; some products are waterproof and provide a vapor barrier.
Creating a Balanced Layout
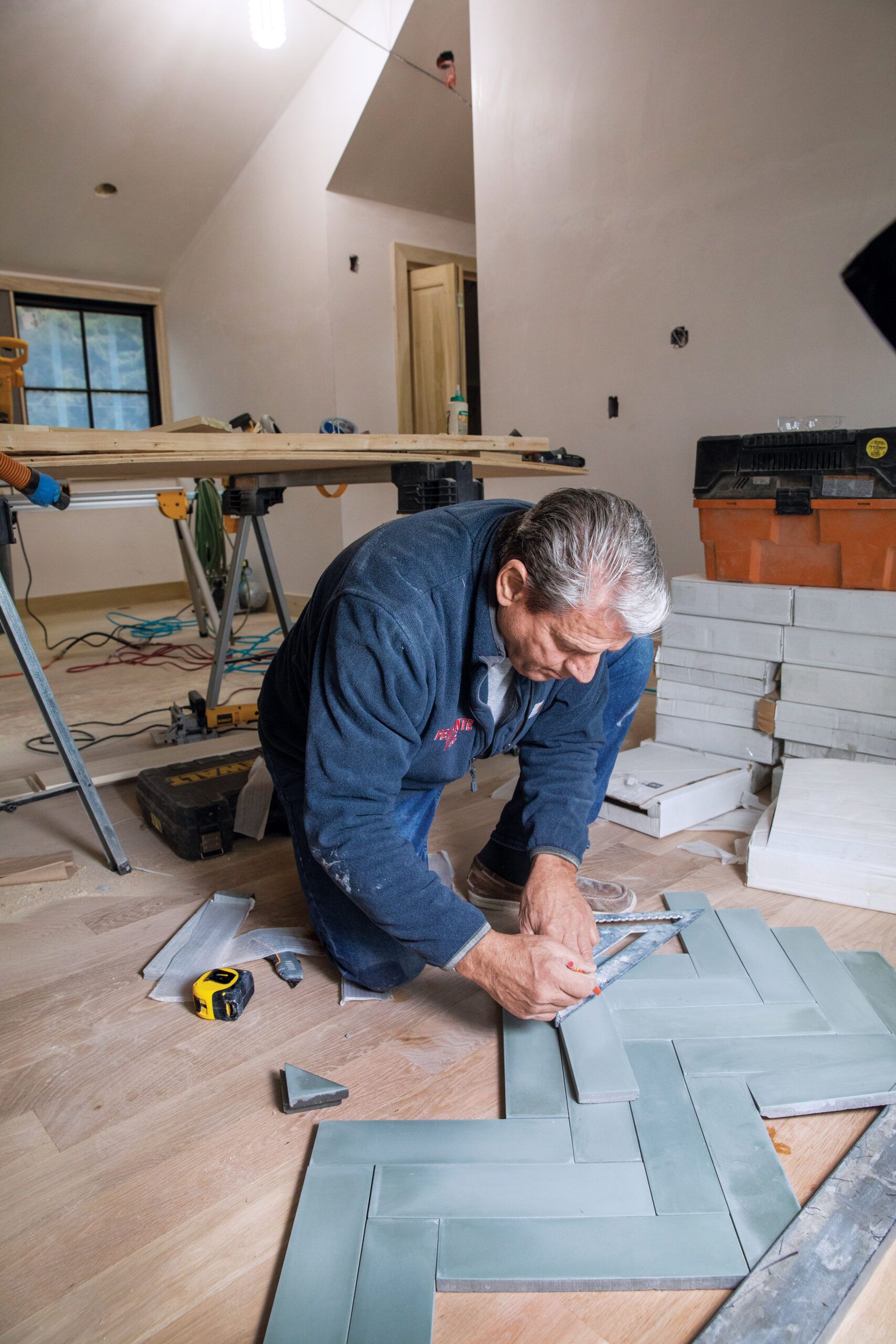
Properly laid tiles are centered in the space, with roughly equal cuts on opposing sides. Here’s how to plan a layout.
- For a floor installation, start by creating two perpendicular reference lines that intersect at the center of the room. They should be perfectly square to each other in order to avoid crooked tiles and uneven cuts. First, mark the center of one wall, then mark the center of the wall across from it. Snap a chalk line between them on the floor.
- Mark the center of the chalk line; this is where a second perpendicular line will bisect it. Draw the bisecting line with a pencil, using a framing square to make sure it’s square to the chalk line.
- In spaces that are 60 square feet or more, the average framing square won’t be big enough to make accurate reference lines. Instead, use a laser level. Snap the first chalk line as described in Step 1 and mark the center, then place the laser level there to create the second bisecting line.
- For a wall installation, use the largest level that fits in the space, or a laser level, to draw level and plumb bisecting lines.
- Do a dry layout on the floor: Start at the point where the two reference lines intersect and move out to the walls. For wall installations, transfer the dimensions to plywood laid over sawhorses and do the dry layout there. This is your chance to evaluate the layout and the cuts that will be needed.
How to Avoid Awkward Cuts
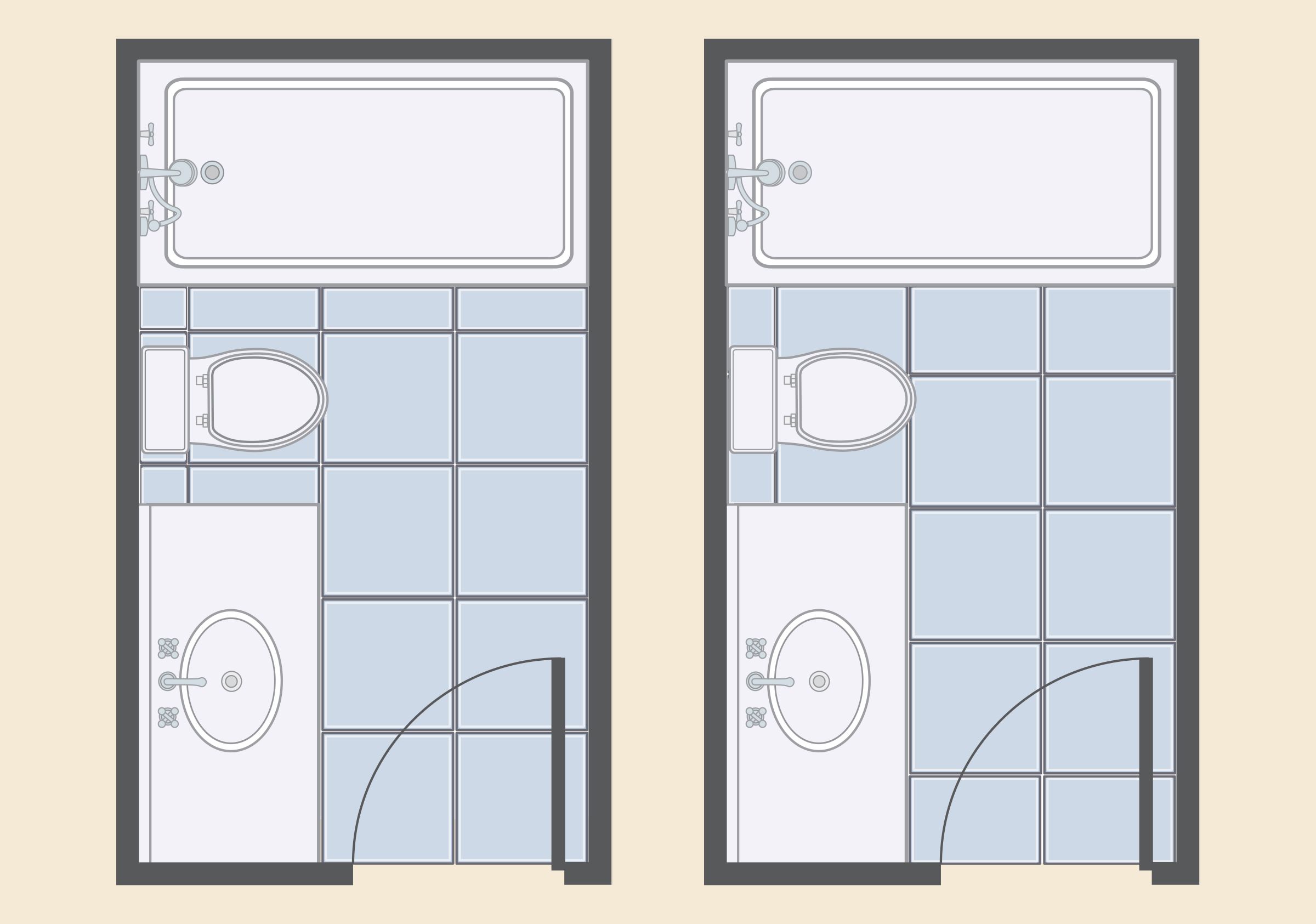
Doing a dry layout allows you to check the size of the cuts that you will have to make. If you’re going to be using less than half a tile or mosaic sheet along an edge, shift the chalk line that runs parallel to that wall by half a tile. You’ll even out the cuts along the opposing walls, and the job will look better with larger tiles along the edges.
Proper Tile Setting
Which adhesive should you use?
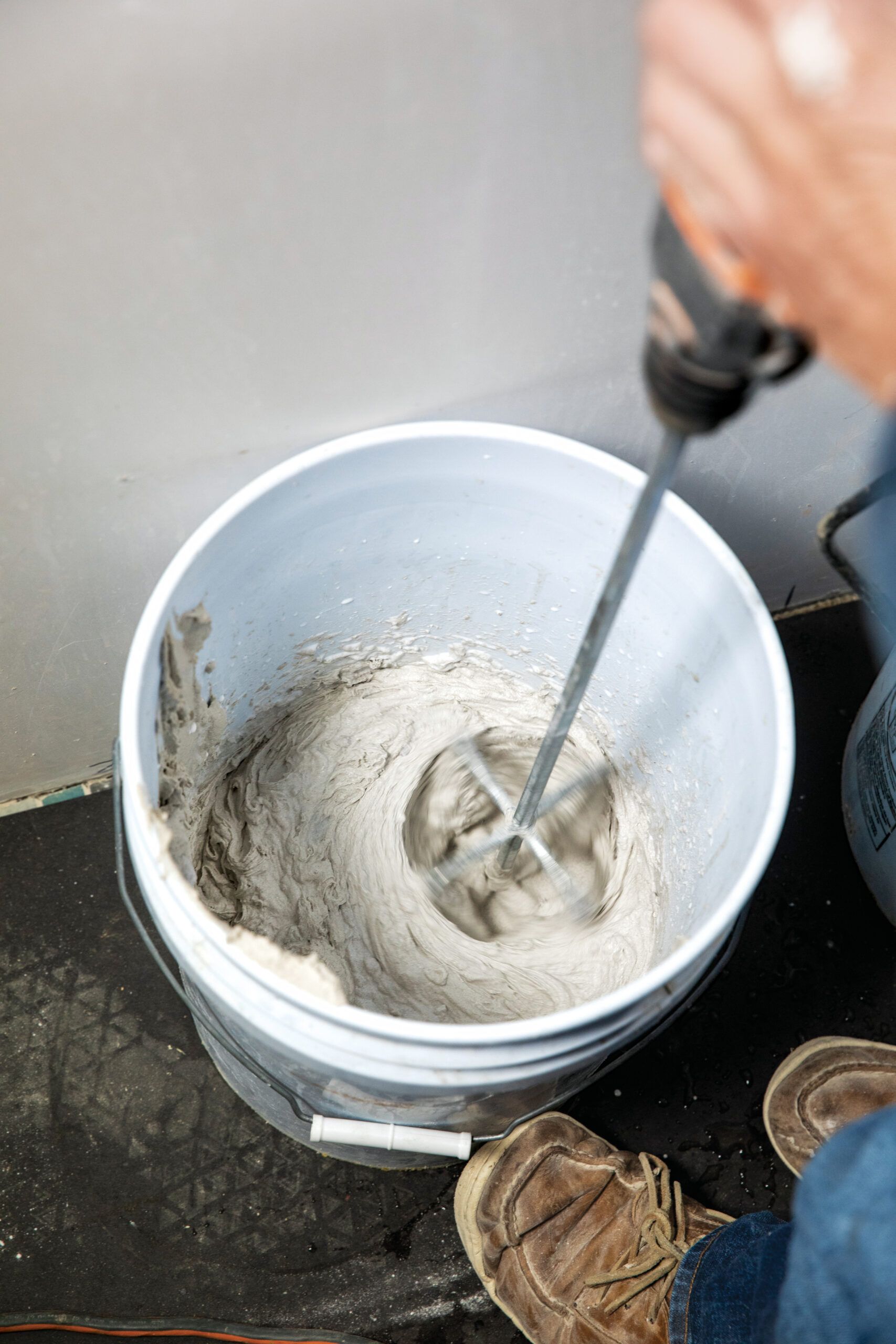
Also known as the bond coat, this is the glue that fastens the tile to the underlayment
- Thinset (versatile and reliable): The tiling standard, thinset is sand-and-cement mortar. Although it’s not waterproof, it’s safe for use in damp areas. But it may not be appropriate everywhere: With a porous—or as tile setters say, “thirsty”—concrete-based underlayment and a hard porcelain tile, thinset may not cure properly because the moisture gets pulled into the underlayment.
- Modified Thinset (a bit more effort but worth it): Mixing thinset with a latex polymer liquid instead of water slows down the curing process, resulting in a stronger bond with any tile.
- Mastic (DIY-friendly, but not for floors): This is a latex-based adhesive that comes conveniently premixed. It doesn’t dry as hard or as fast as other adhesives, so it’s not great for floors, but it works well for many wall applications.
- Epoxy Mortar (bulletproof but for pros only): A combination of epoxy and sand-based powder, this mortar is incredibly durable and stain resistant, and it’s required with some nonporous glass and stone tiles. But it’s hard to trowel, quick to cure, and tough to remove if it gets somewhere you don’t want.
How to mix thinset
Follow these steps to ensure it holds well.
- Mix the entire bag. Don’t try to use partial bags—it’s too difficult to get the proportions exactly right.
- Put the water or latex additive in the bucket first. Adding the powder to the liquid helps avoid dry spots.
- Follow the manufacturer’s directions exactly for the mixer’s rpm and how long to let the thinset slake, or rest, before using it. Otherwise the bonding strength could be compromised.
- Once it’s mixed, don’t add more water, which will weaken it. Keep a dampened rag over the top of the bucket to slow curing, and remix the batch if it starts to stiffen.
What is back buttering?
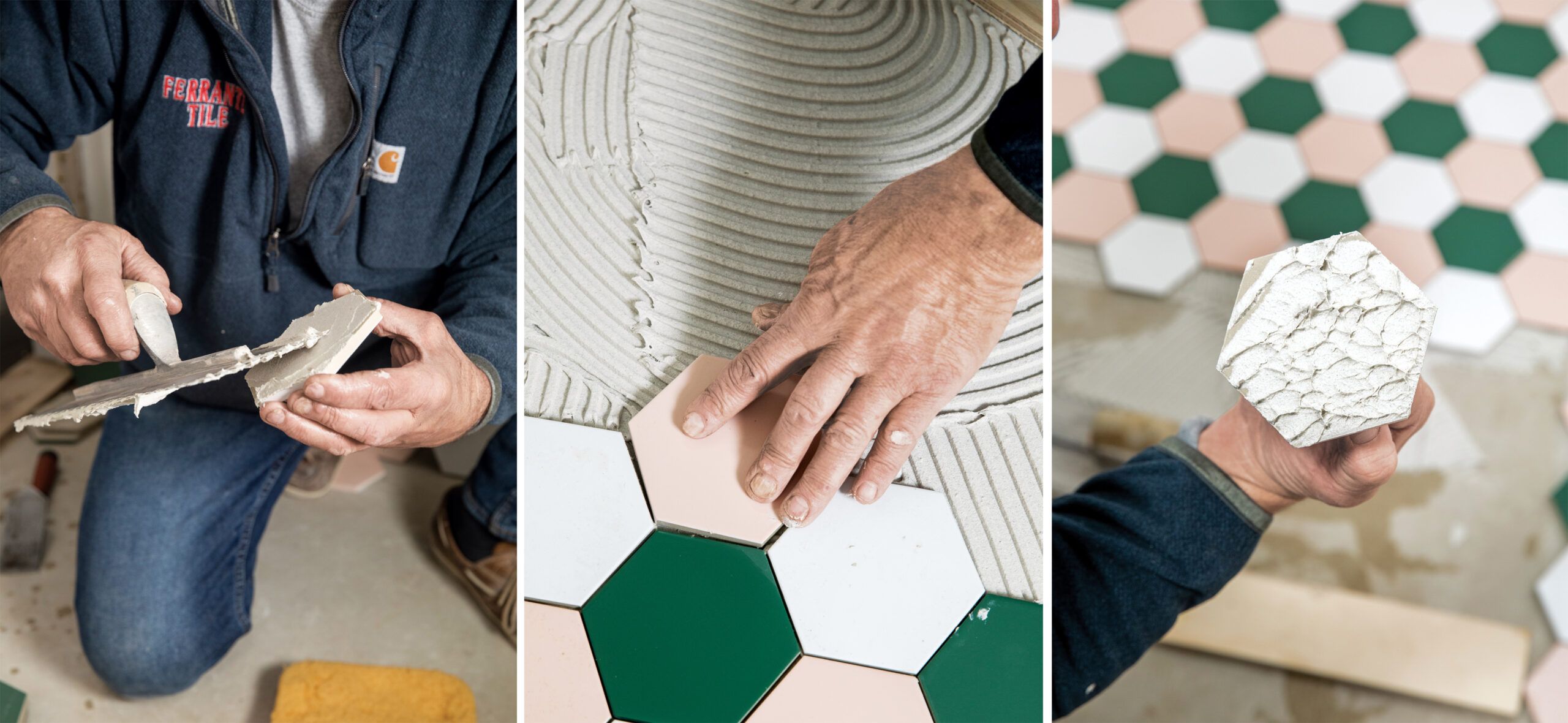
This technique, recommended for natural-stone tile, eliminates air bubbles to ensure a superior seal. While not every type of tile requires it, Mark often takes the extra step to make sure his tile job is rock-solid
After spreading a layer of adhesive onto the underlayment with a notched trowel, use the trowel’s flat edge to apply a thin coat of adhesive to the back of a tile.
Set the tile in place using firm, even pressure
Check your work by pulling the tile up. At least 80 percent should be covered with adhesive—or 95 percent for wet areas. You shouldn’t see ridges from the notches—it should look like a choppy ocean.
Tips for Installing Tile
What is the best way to cut tile?
There are several tools you can use, but a wet saw is the most versatile and gives the cleanest cuts, Mark says. Rental units often come with dull blades, which will slow down your work and can chip the tile. Mark’s tip: Buy a new blade for the rented saw; it will cost about $50 to $100.
When to use caulk or grout
Whenever tile meets another surface—where the kitchen countertop meets the backsplash, or the edge of the tub touches the tile surround—the seam should be sealed with caulk, not grout. If you use grout, it will eventually crack and fall out as the different materials shift independently of each other. Most installers will leave this joint empty, carefully working around it, and then, once the rest of the area is grouted, fill the seam with silicone caulk as a final step. But it can be difficult to keep grout out of that seam, so Mark recommends an easier approach: Lay down a bead of caulk first, then bed the first course of tiles in it.
Make mesh-backed mosaic sheets look seamless
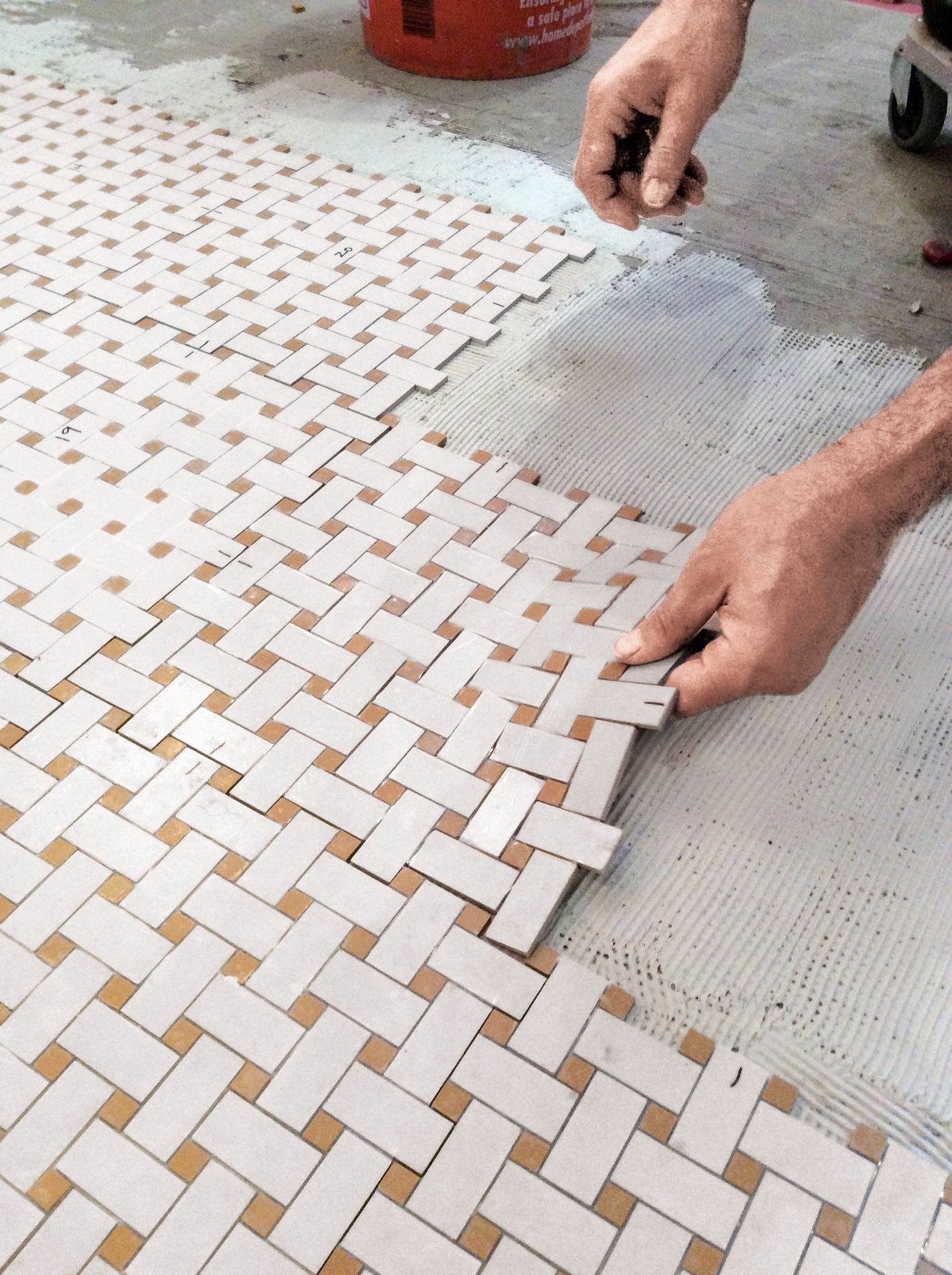
The most common flaw with mosaic tile installations: visible lines where the sheets meet. Here are some tips for avoiding them
- Take your time to dry-fit the sheets together to achieve perfectly even spacing. This may involve trimming away some of the mesh.
- If the spacing is off at all, “you might need to peel off a tile here and there and lay it independently,” Mark says.
- If the design of the tile allows, cut some sheets in half, clipping around the tiles themselves, and stagger them in the layout to eliminate any long, continuous seams.
Easy backsplash installation
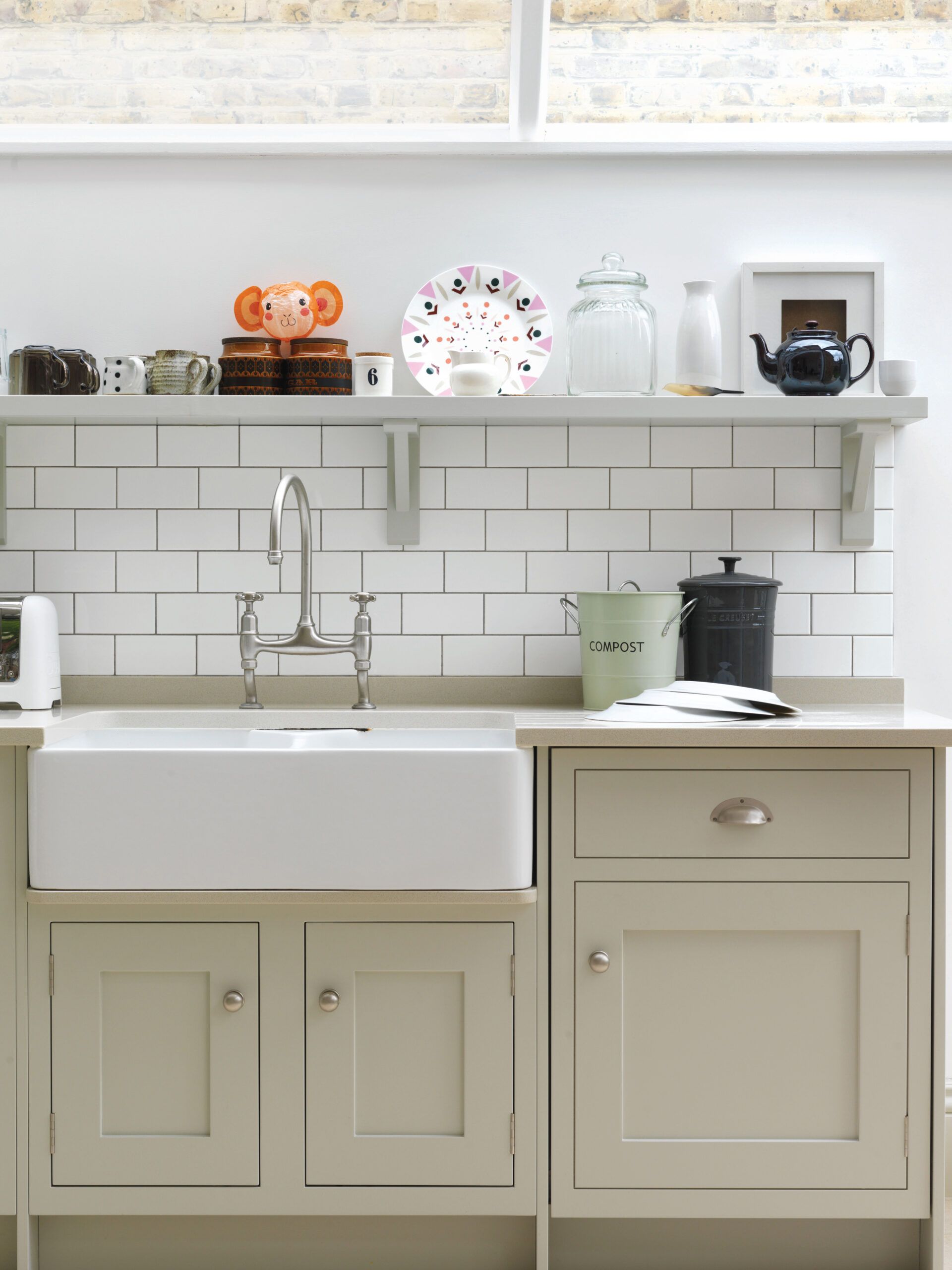
To help avoid complex cuts, use 3-by-6-inch subway tiles—they’re perfectly sized so you can run full courses at the standard 18-inch height of the backsplash. For other tile, there are two approaches: Start with a full course at the bottom and trim the top row, which isn’t as visible when standing in the kitchen, or opt for an even layout with the same cuts to the top and bottom courses.
Pro Tip: “It’s common to see slight variations in color and texture from one box of tile to the next, so you should always mix them up. I open three or four boxes, pull a handful of tiles from each, and stack them up. Then I grab tiles randomly from each pile as I work, and keep opening boxes and adding to the piles as I go.” -MARK FERRANTE
How to get tiles flat and even
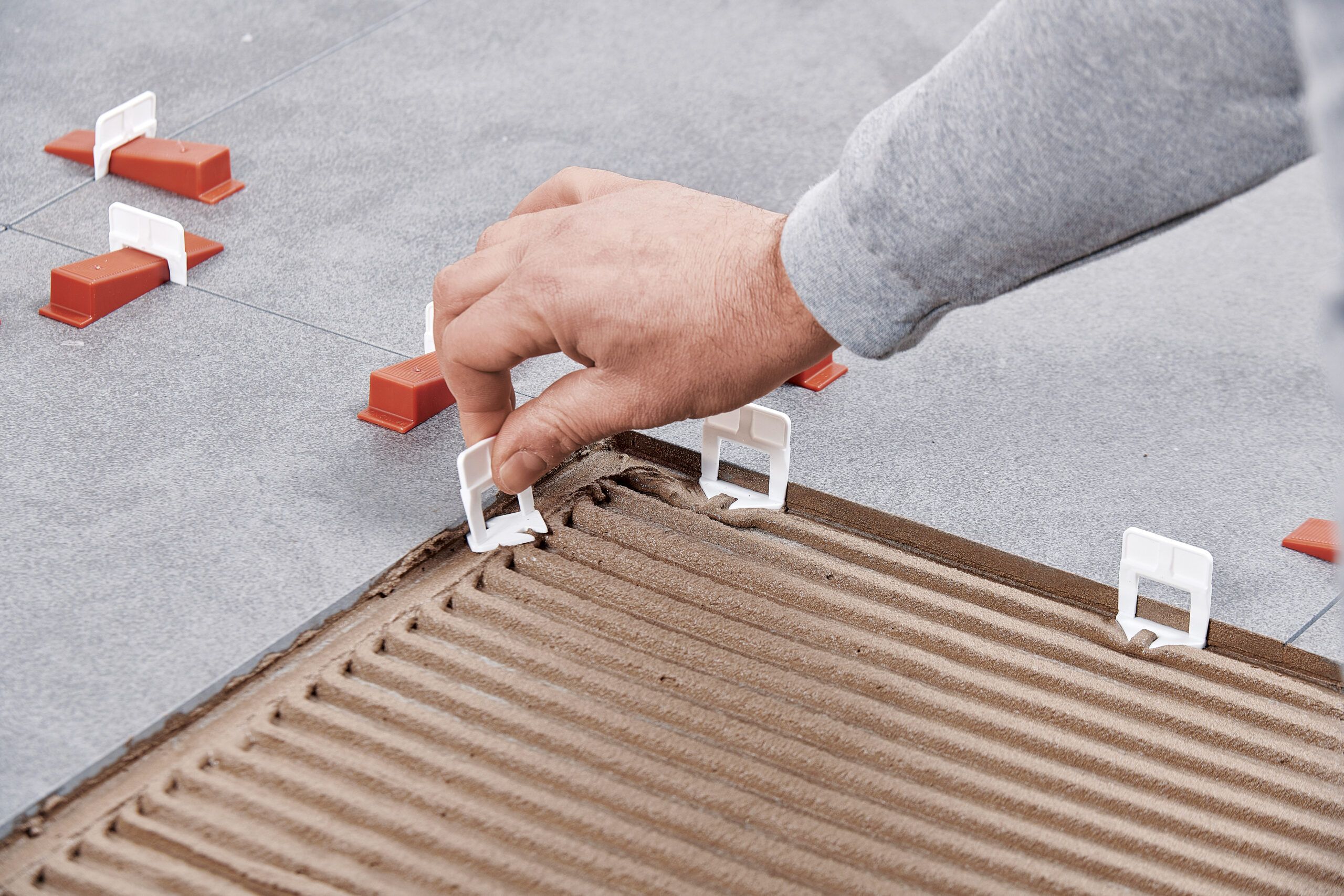
Lippage is the industry term for when a tile juts out higher than the one next to it. Lippage can be an eyesore, particularly on a backsplash where undercabinet lights highlight the resulting shadow lines, and it creates a tripping hazard on a floor. It can happen when the underlayment isn’t perfectly flat or tiles are warped or irregularly sized— problems you may not be able to prevent.
What you can do is use a tile-leveling system that pulls neighboring tile edges into alignment while the adhesive cures. Thin plastic clips are placed under tiles, wedges are inserted to line up adjacent edges, and later, the clips snap off. Mark likes the Raimondi Leveling System shown here ($64; amazon.com).
Working with large-format tiles
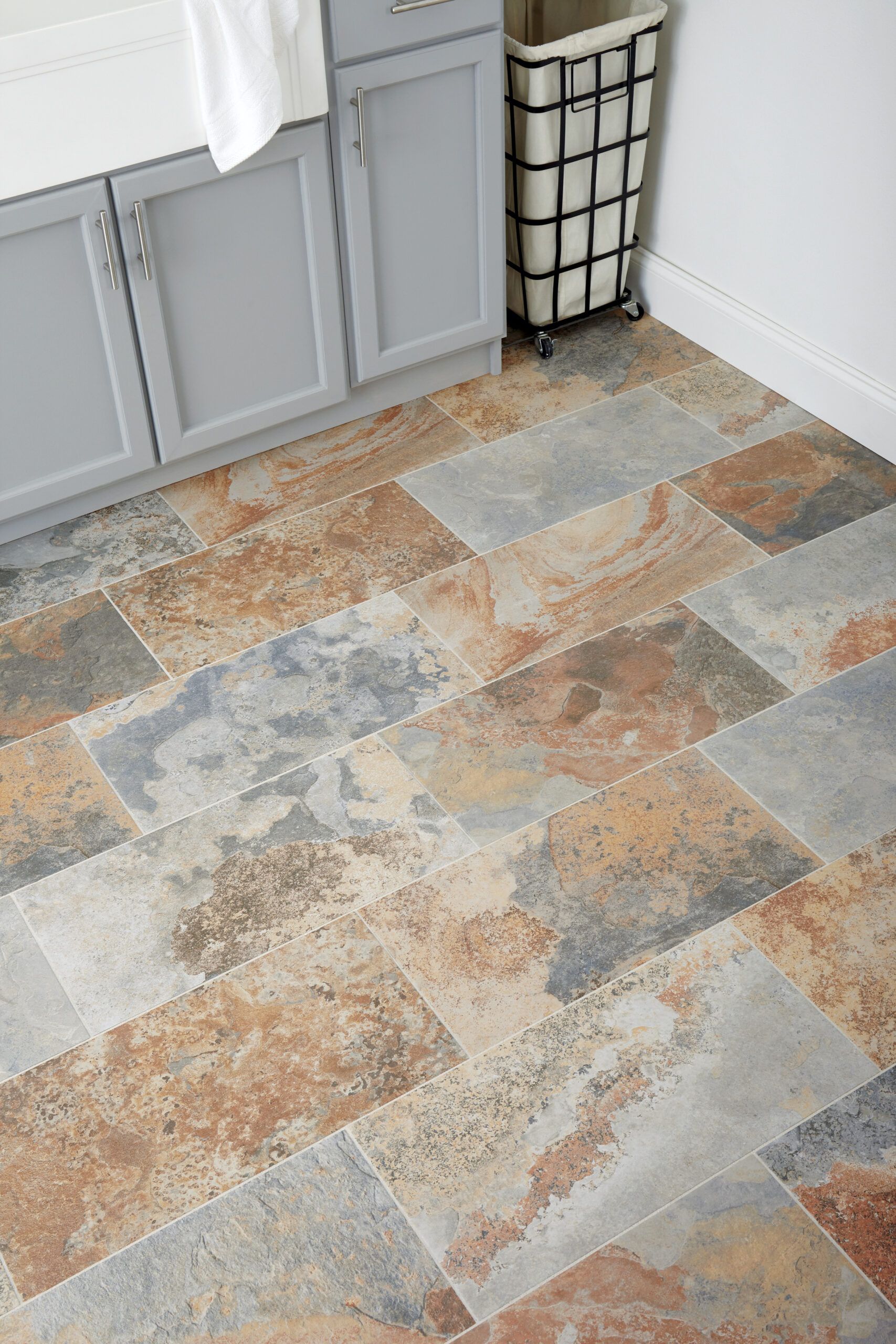
Some of today’s most popular tiles come in sizes like 12 by 24 inches and 6 by 36 inches. That changes the installation game in a few important ways
- Even slight imperfections in your floor or wall can cause significant unevenness with large-format tiles. Use self-leveling underlayment on floors and patching compound on walls to get a flat surface to work with.
- Use a heavier thinset, known as large-tile and heavy-tile mortar, and deeper notches in your trowel to get better coverage underneath the tile. Consult your tile supplier or manufacturer for exactly what your tile needs.
- Offset tiles by 33 percent instead of 50 percent in a running-bond pattern (as shown above). Larger tiles are often bowed, and this pattern means you won’t be placing the highest part of one tile, the middle, next to the lowest part of another, the end.
- Plan your layout carefully, keeping in mind that you’ll need to find a happy medium between making equal cuts on opposite sides of the room and not wasting too many large, expensive tiles.
How to hide unfinished edges
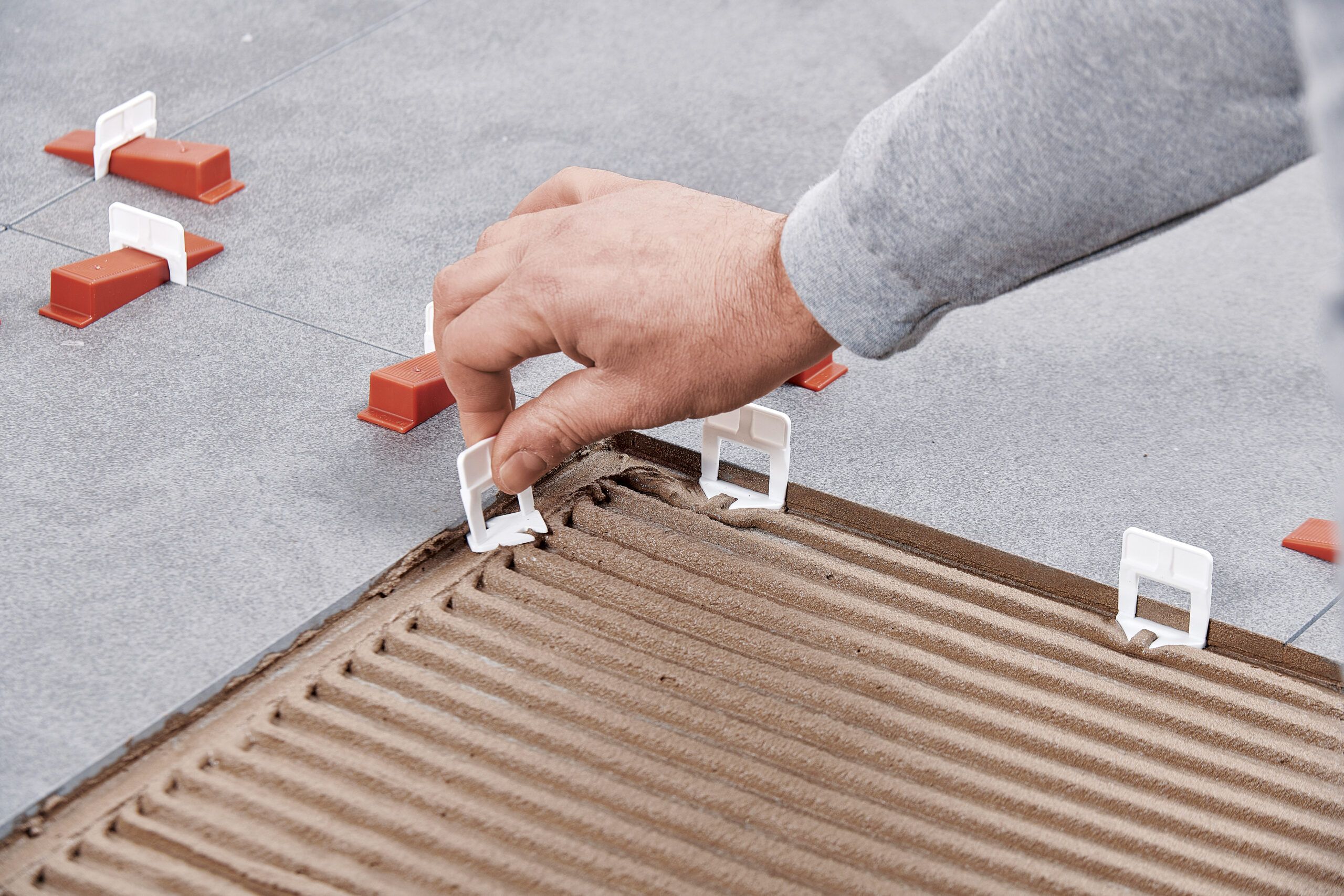
If your choice of tile isn’t available with a bullnose or finished edge, a pro can use a special profile wheel on the wet saw, or an angle grinder, to round the edge of most stone tiles such as marble and granite—and many porcelain ones, too. This is not a DIY job, but a local stone retailer may do it for you.
ANOTHER OPTION: Create a finished border with wood strips or use aluminum edging profiles, such as those made by Schluter, which get embedded under the tile and have a sleek look.
Grout: The Finishing Touch
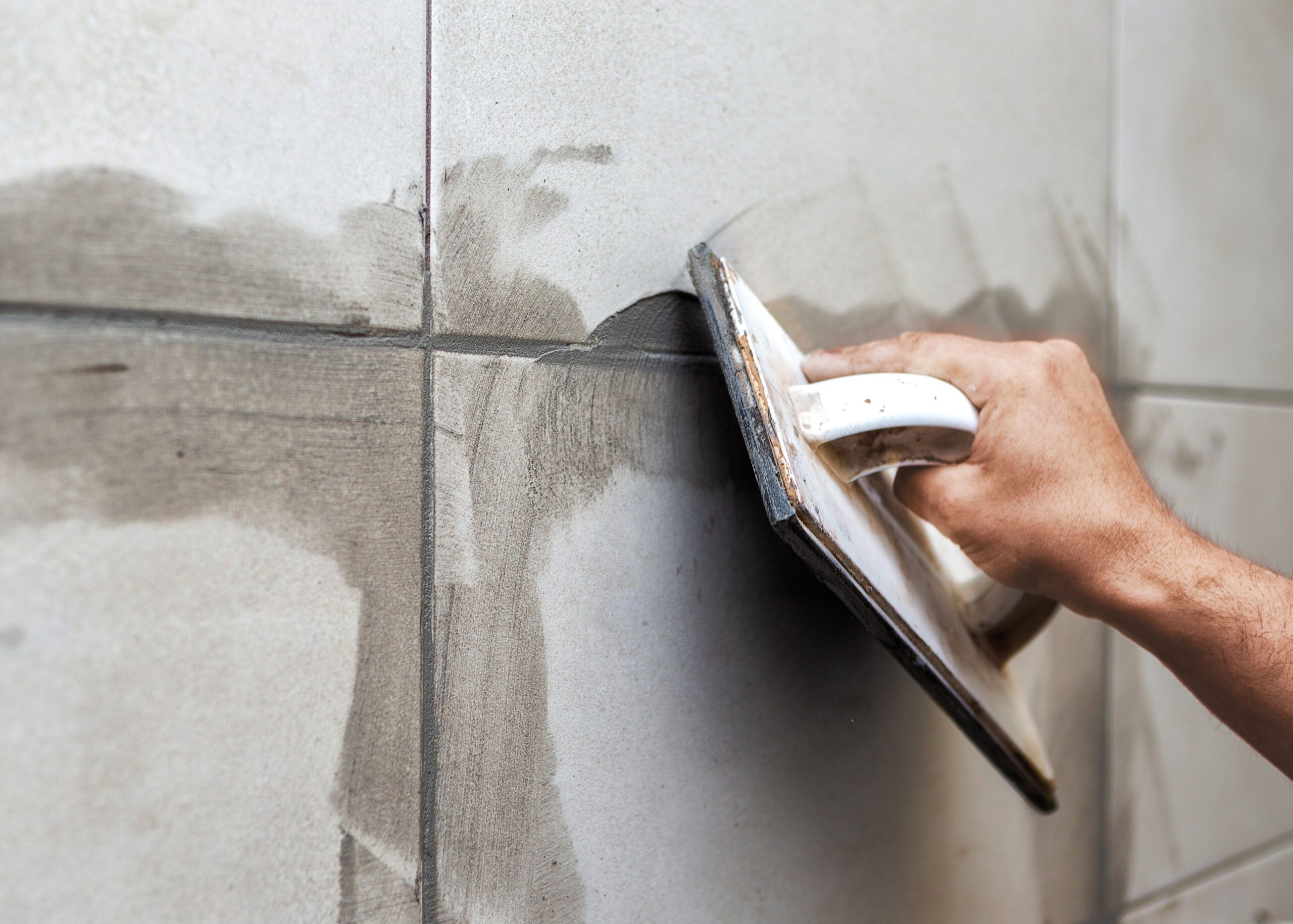
Picking the right type of grout
When deciding which grout is best for your project, consider how often it will be exposed to water, dirt, and spills. A basic grout is fine for low-traffic areas, but for rooms like the kitchen, a grout with built-in stain resistance is a better choice:
Cement grout: Best for walls
Inexpensive and easy to work with, it comes sanded—best for joints 1/8 of an inch or larger—or unsanded, which is best for narrower joints. But it’s prone to cracking, offers only minimal stain resistance, and requires periodic sealing.
High-performance grout: Best for floors:
Added polymers give this cement grout better stain resistance and more consistent color while helping prevent efflorescence, where salts rise up and whiten the grout over time. Seal it once or twice per year.
Premixed polymer resin: Best for bathrooms and mudrooms
Also known as single-component or ready-to-use grout, this acrylic- or urethane-based product comes premixed and doesn’t require a sealer. It stands up to moisture and stains and offers dependable color consistency.
Epoxy: Best for any area or the house
Epoxy grout never needs sealing, won’t absorb water, and doesn’t stain or darken over time. But it’s stickier and sets faster than other types of grout, so application can be more challenging.
Minimizing grout lines
Grout makes a tiled surface stronger and helps keep out dirt and water, but “there’s nothing pretty about it,” says Mark. “The tighter the grout joints, the better the tile job looks,” he says. He likes to go as small as 1/32 of an inch, but that requires skill, since tiny grout joints leave little room for slight differences in size and shape from one tile to the next.
You could end up with two tiles that are touching, or not get any grout in the joints at all. Novice installers who want to play it safe shouldn’t go smaller than a 3/16-inch grout joint. Using tile spacers can make it easier to set tiles the same distance apart.
Tips for a better grout job
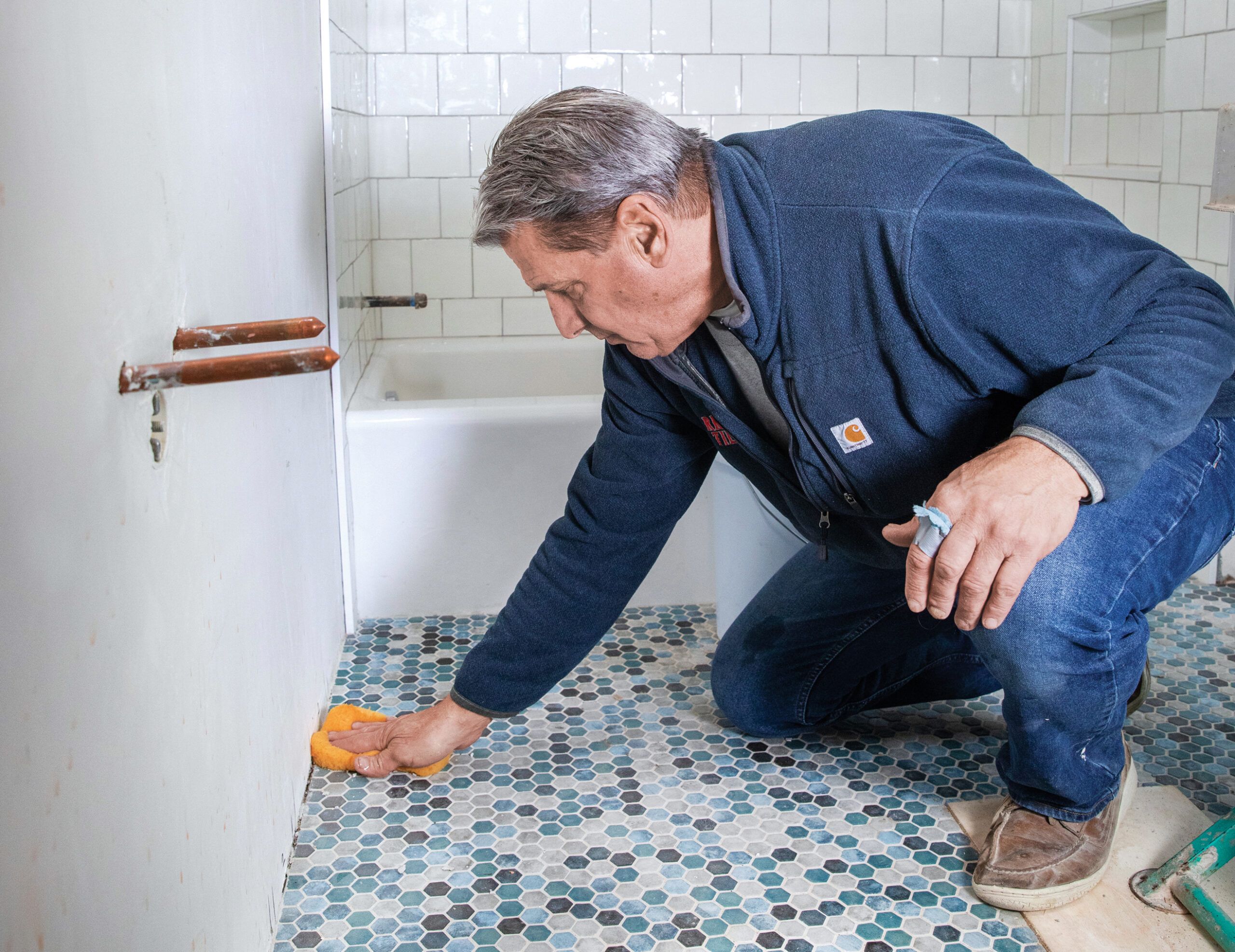
- Mix the grout exactly to the manufacturer’s instructions, always using the whole bag and always starting with the water.
- Spread it over the tile and grout lines—or just over the grout lines with large-format tiles—with a grout float recommended for the type of grout you are using. Hold the float at a 45-degree angle to the tile surface, and press the grout into the joints.
- Allow the grout to set for the manufacturer-specified time. Cover only as much area as you can get back to before the setting time has elapsed. Some premixed polymer resins set in 30 minutes or less, and they will stick to the face of the tile if you don’t wipe them in time.
- Wipe the tile clean with a slightly damp sponge, being careful not to add any water to the grout lines; that could wash out pigment and interfere with the grout’s curing process. If any grout pulls up out of the joints, stop and let it set longer.
- Check that the surface of the tile is completely clean of grout before leaving it to cure overnight.
When to seal grout and tile
Sealing protects against wear and tear and makes it less likely that spills will work their way into the tiled surface. A sealer can’t completely prevent stains, however. “It just gives you a little more time to clean up Aunt Mary’s spilled wine,” says Mark. Here’s what you need to know
To seal or not to seal? Check with the manufacturer, but in general, porous tiles such as marble and unglazed ceramic require a sealer. Cement grouts need to be sealed even if the tile does not. Glass tile, glazed ceramic tile, high-gloss porcelain tile, and epoxy, acrylic, and urethane grouts do not need sealing.
How often? Reseal every 6 to 12 months, depending on how much use the area gets and what kind of tile it is.
What kind? “Doing the job right starts with purchasing a premium, water-based penetrating sealer,” Mark says. Look for one designed for your tile or grout; you may need to request it, since often only the low-cost sealers that consumers are likely to buy are displayed. His bottom line: “If you’re not paying at least $30 for a quart, don’t bother buying it.”
Directory
Thanks to Scott Carothers, director of certification and training for the Ceramic Tile Education Foundation; ceramictilefoundation.org.
Ian O’Connor, product manager at Custom Building Products; custombuildingproducts.com.
Andy Acker, director of education at Schluter Systems; schluter.com.