Repair Rather Than Replace
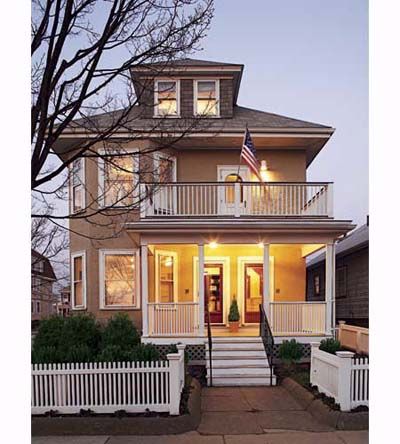
Nothing on This Old House‘s East Boston project house seemed in worse shape than the stucco siding. Years of harsh winters had left giant cracks and gaping holes in the masonry surface. Making it worse was the ivy working its way into the cracks, opening a path for water to get behind the stucco. A complete replacement would have come in at $50,000.
Instead, after the ivy came down, a masonry crew patched the worst sections with new stucco over wire lath, then filled remaining cracks with caulk. Tom’s crew cleaned the entire surface using grinders fitted with wire wheels. Then painters applied a primer and two tinted layers of an elastomeric coating—basically a thick acrylic paint—which helps tie everything together and give it a smooth finish. The repairs cost $10,000.
What They Saved: $40,000
Roll Up Your Sleeves
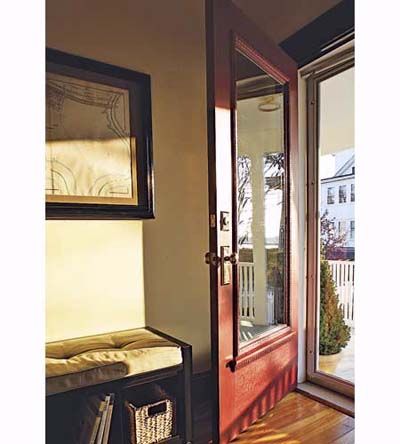
The original front doors to the house (which had been in the basement for decades) were a bit the worse for wear. But that didn’t mean they couldn’t be spruced up. Chris and Liz stripped the original finish themselves, then Tom and TOH master carpenter Norm Abram reglued some joints and patched the worst spots with epoxy. Some new tempered and insulating glass, and the elegant 1916 doors with egg-and-dart detail were ready for action again, for only $480 in materials. Similar new doors could have cost $2,000.
What They Saved: $1,520
Limit Demolition
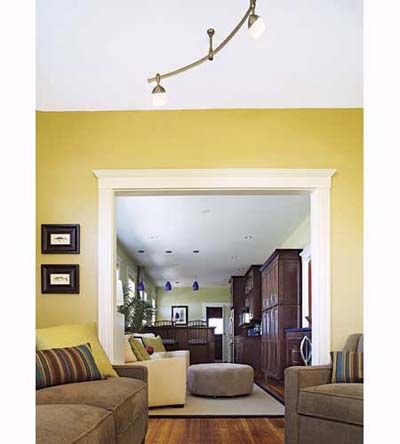
Because the entire house needed new wiring and insulation, on the first floor it was cost-effective to remove the cracked plaster ceilings to gain access. But Tom opted to leave the original wood lath in place, then wallboard over it. This saved on labor for sorting the debris, cleaning it up, and pulling all the nails left in the joists, and it reduced dumping fees.
What They Saved: $600
Rob Peter to Pay Paul
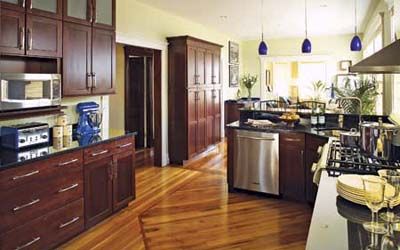
When Tom took down walls to enlarge the kitchens in both apartments, he had to contend with floorboards from adjoining rooms running in different directions, as well as missing flooring where the walls had stood. Seamlessly weaving in patches would have been very labor intensive, and the new wood wouldn’t have matched anyway; replacing with equivalent reclaimed heart pine throughout both kitchens would have cost about $26 a square foot for materials and labor. So Tom got creative.
In Liz’s kitchen, he cut the flooring at an angle in the middle of the room to echo the corner cabinet. Then he carefully pulled up all the boards on one side of the cut and relaid them on a diagonal. To salvage some extra flooring, he took boards from where the washer/dryer and the cabinets would go. In Chris’s kitchen, he pulled up all the boards that were turned the wrong way and relaid them so the floor would be uniform.
Replacing the floors would have required the same demolition, installation, and refinishing, plus the cost of new materials. So the only added labor here was the extra 2½ hours it took to pull up the boards without destroying them.
What They Saved: $16,000
Use Luxuries Selectively
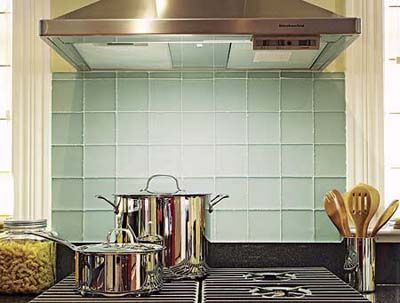
A glass-tile backsplash is a beautiful detail in any kitchen, but installing one throughout could have set Liz back $1,500. The place where a backsplash was most necessary, however, was over the stove, to make cleaning up cooking splatters easier. Tiling only this 2-by-3-foot space cost her a doable $250.
What They Saved: $1,250
Adjust To Your Circumstances
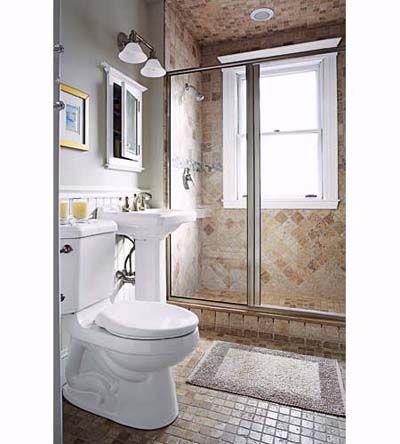
Tom isn’t a fan of windows in a shower because, as he puts it, “you have exterior conditions—rain and heat—on the interior.” But in the case of the first- and second-floor bathrooms he had no choice; there was no room to move the openings and no budget for new windows set higher up on the wall. Removing them and closing up the walls would have cost $800 per window. So he created all-weather protection for the existing wood sash by painting them with exterior latex paint and using waterproof PVC, which costs the same as wood but won’t rot, for the window trim.
What They Saved: $1,600
Add Detail With Paint
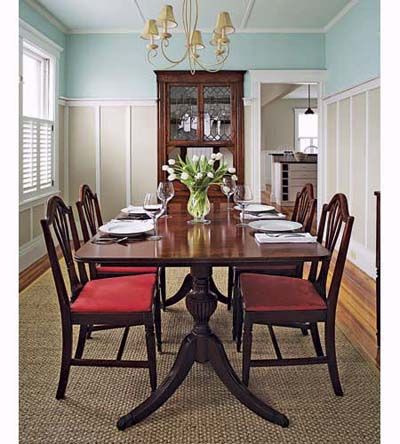
Chris’s formal dining room came with nice top rails and battens on the walls. However, before the remodel, the trim was finished in a dark stain and just looked like applied molding on the white walls. By painting the moldings white and the spaces in between them a coordinating warm beige—different from the pale-blue field above the rail—the bottom half of the wall looks more like it’s actually paneled. Real wood or even MDF paneling for the room would have run as much as $4,000. The paint job was a mere $700.
What They Saved: $3,300
Stick With Stock
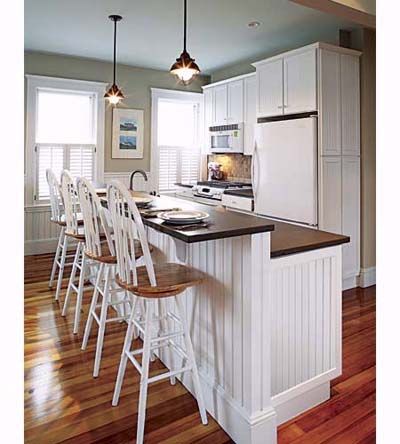
A kitchen can be outfitted for a lot of money—with custom cabinetry and paneled appliances—or for a whole lot less if you order up off-the-shelf items. Chris’s seaside-cottage look was easy to achieve with stock white cabinets and beadboard doors; white appliances blended right in. But even some nice finishing details were created with stock items. The panels on the side of the refrigerator and the island are actually pieced together from affordable stock cabinet doors, rather than custom pieces.
What They Saved: $1,025
Be Open To Open Shelves And Doors
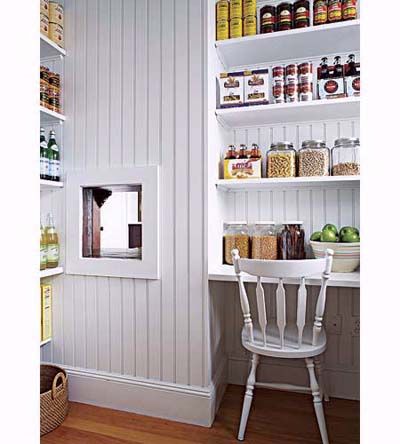
Chris’s old kitchen had a small, doorless room that held the fridge; Tom turned the space into a food pantry, lining it with open shelving and forgoing the lower cabinets often found in pantries (saving $1,000). He also left off the pantry’s entry door (a $350 item). To make the highly visible alcove blend with the rest of the kitchen, he lined the walls with beadboard.
What They Saved: $1,350
Reuse Existing Materials

Liz’s kitchen expansion meant that a built-in china cabinet lost its surroundings. Meanwhile, Chris’s third-floor laundry area needed a linen closet. Rather than toss aside an attractive feature of the original house, Tom repurposed the leaded-glass cabinet front (the sides and back had been the walls) in Chris’s laundry room. New cabinet doors and drawers with that kind of detail would have run upward of $3,700. The labor to move the old cabinet and give it sides and a back cost about $200.
What They Saved: $3,500
Total Savings: $70,145