Project details
Skill
Cost
Estimated Label
Industrial-modern design is everywhere these days, with its blend of warm wood and metal or concrete. Having admired a table with a sleek tapered base and a simple concrete top, I wanted to try my hand at a similar mixed-media build. I was nervous about incorporating concrete into a wood-working project, but I found it easier and less expensive than I had expected.
With a $20 water-heater drip pan and a bag of concrete mix, I successfully cast a tabletop on my first try, with enough leftover material to make two more. I learned that a spritz of a release agent makes it easier to pop the top out of its form, and sealing the cured concrete with paste wax yields a soft, powder-free finish that resists water stains.
For the base, two interlocking leg frames ensure a sturdy platform, and a coat of stain dresses up the stock lumber. Best of all, the finished side table has exactly the kind of clean, industrial-modern look I was after.
Getting Started: Building a Concrete End Table
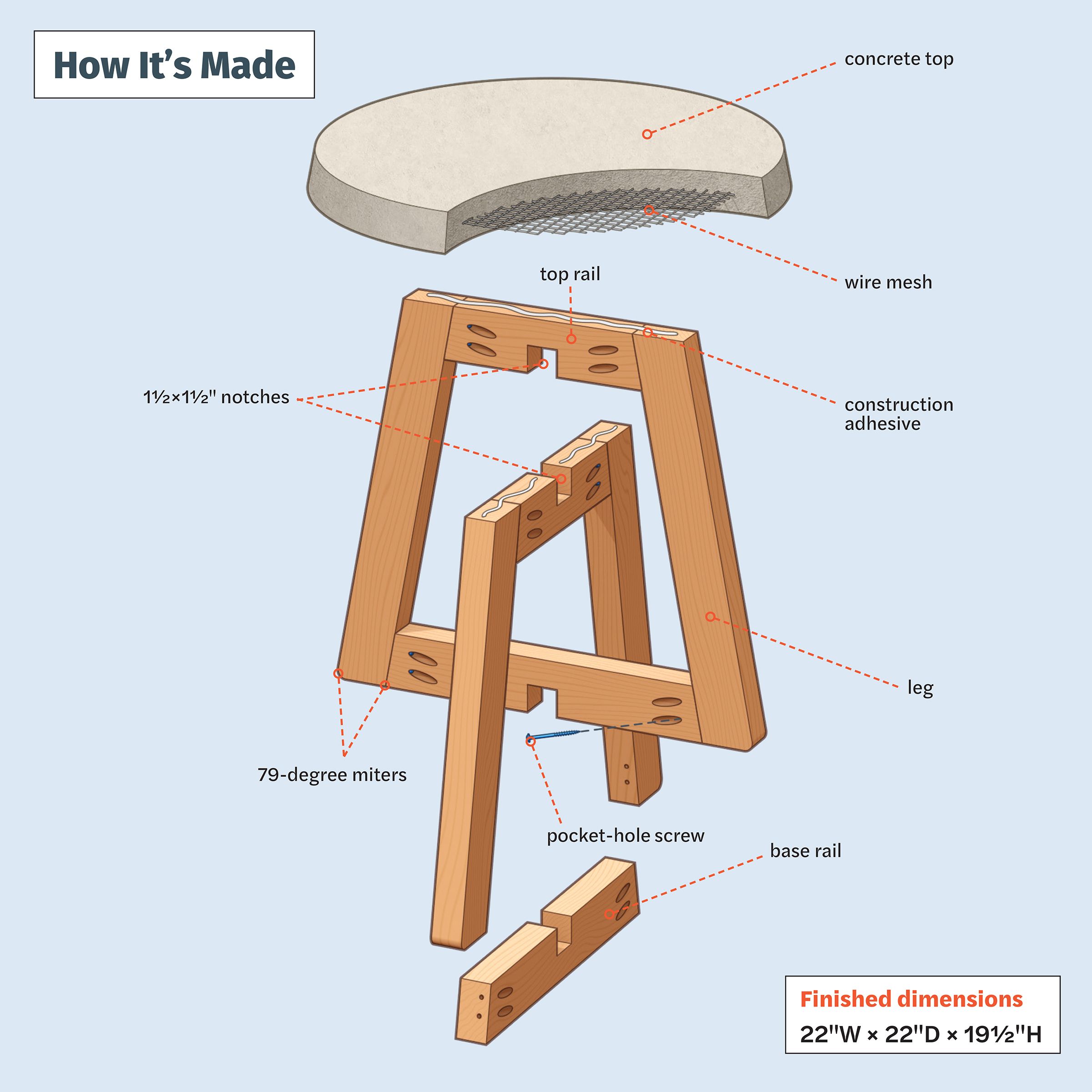
You can make the tabletop with a general-purpose concrete mix, but I opted to upgrade to a countertop mix, which contains finer aggregate that results in a smoother surface, plus specialty additives that make the cured concrete stronger. I chose a standard gray mix for this project, but countertop mix is also available in white, which can be tinted with powdered or liquid pigments to create a wide range of colors.
When choosing a form, look for one with a smooth interior that can be disassembled or one made of a slightly flexible material to facilitate removal. My metal pan’s thin bottom flexed enough to pop out the top once the concrete dried. Last, to lessen the chance of the concrete cracking, I recommend reinforcing the top with a piece of wire mesh cut 2 inches smaller than the diameter of the form.
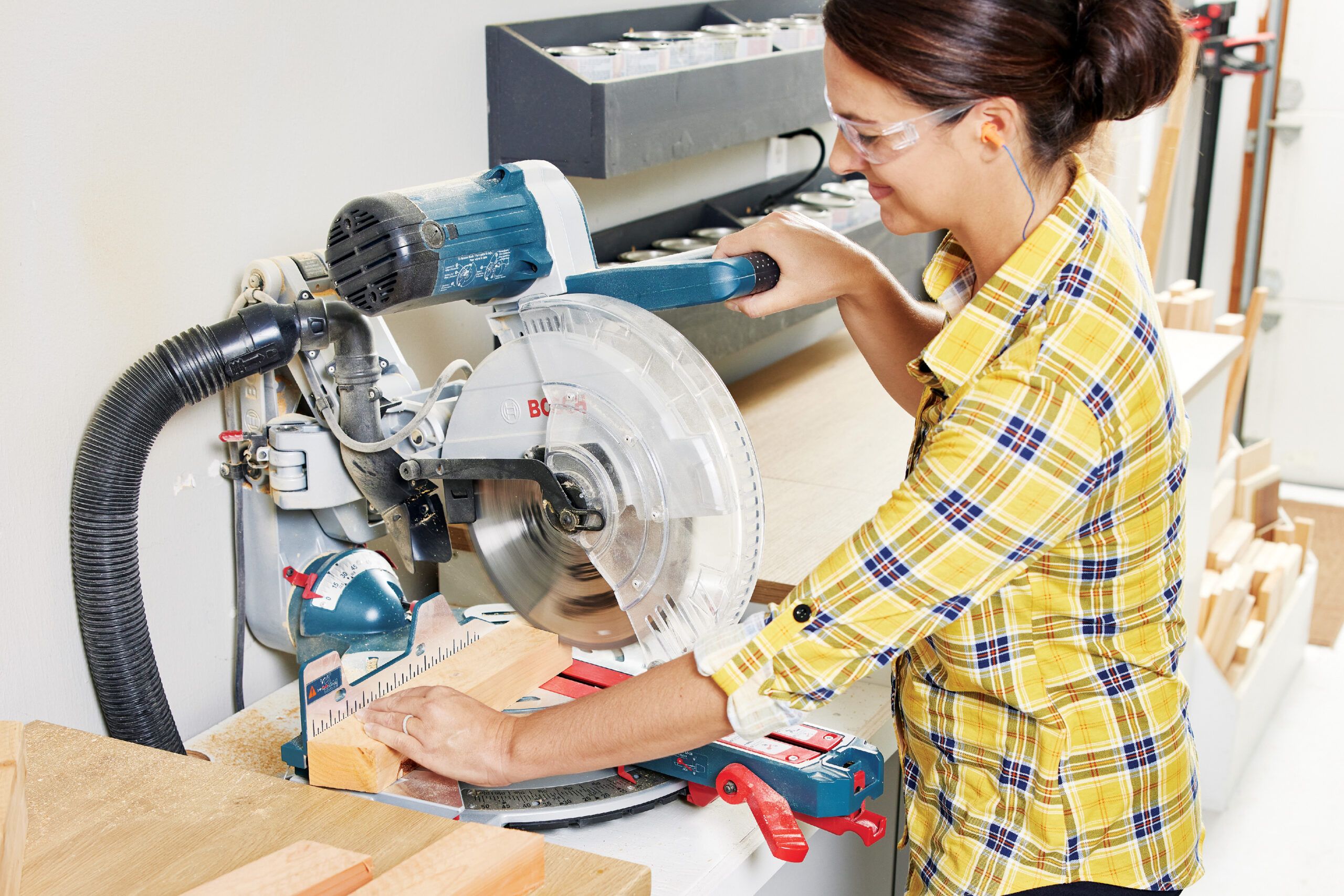
Cut list
- 2×3 top boards – 2 @ 10” (ends mitered at opposing 79 degrees)
- 2×3 side boards – 4 @ 18 3/4” (ends mitered at parallel 79 degrees)
- 2×3 bottom boards – 2 @ 16” (ends mitered at opposing 79 degrees)
Steps for Building a Concrete End Table
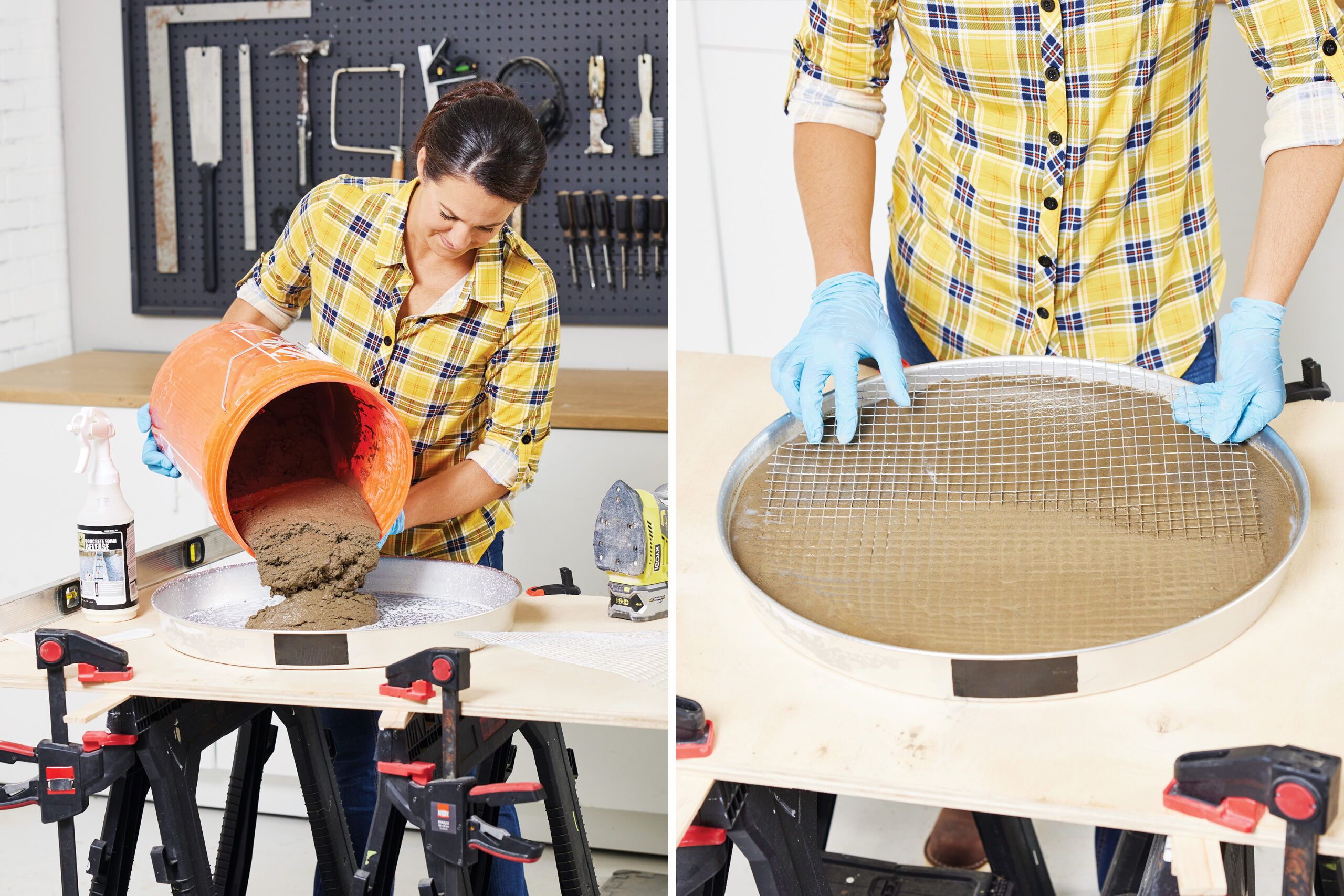
1. Mix and pour the concrete.
Duct tape any openings in the form—my pan had a drain hole—on both sides, set it on a level surface, and then coat the inside with a release agent. In a 5-gallon bucket, combine about 1/3 bag of concrete with water, and use a drill/driver fitted with a mix- ing paddle to blend till it has a peanut butter–like consistency. Pour the concrete into the pan.
2. Reinforce the top.
Cut the wire mesh about 2 inches smaller than the pan’s diameter. Submerge the mesh about halfway into the concrete. To release bubbles in the wet concrete, set an orbital sander (skip the sandpaper) against the sides and underside of the pan.
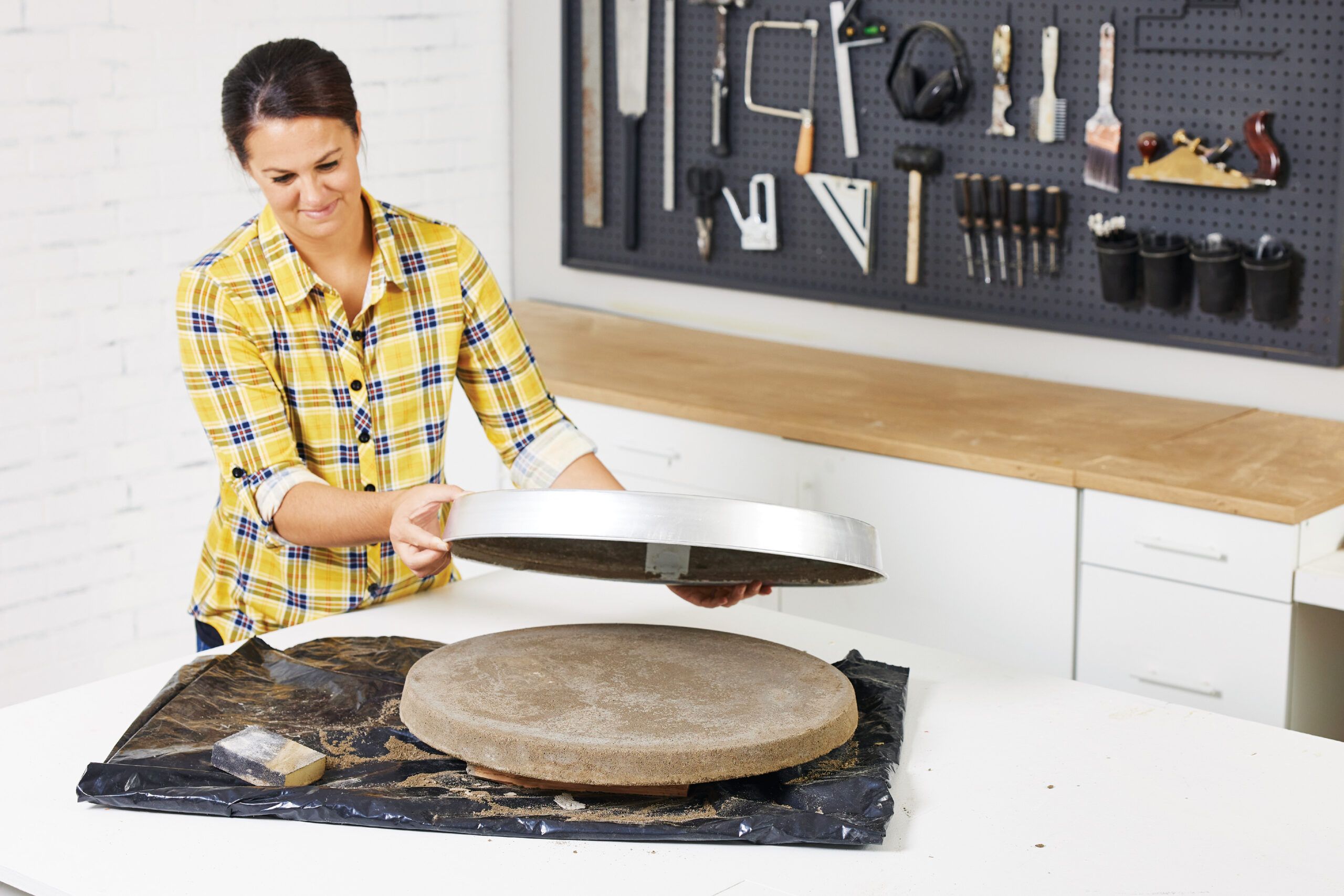
3. Remove the form.
After about 24 hours, free the top from the pan and set it on scrap blocks to encourage it to continue drying. To smooth the top, wet-sand the concrete with a sanding sponge.
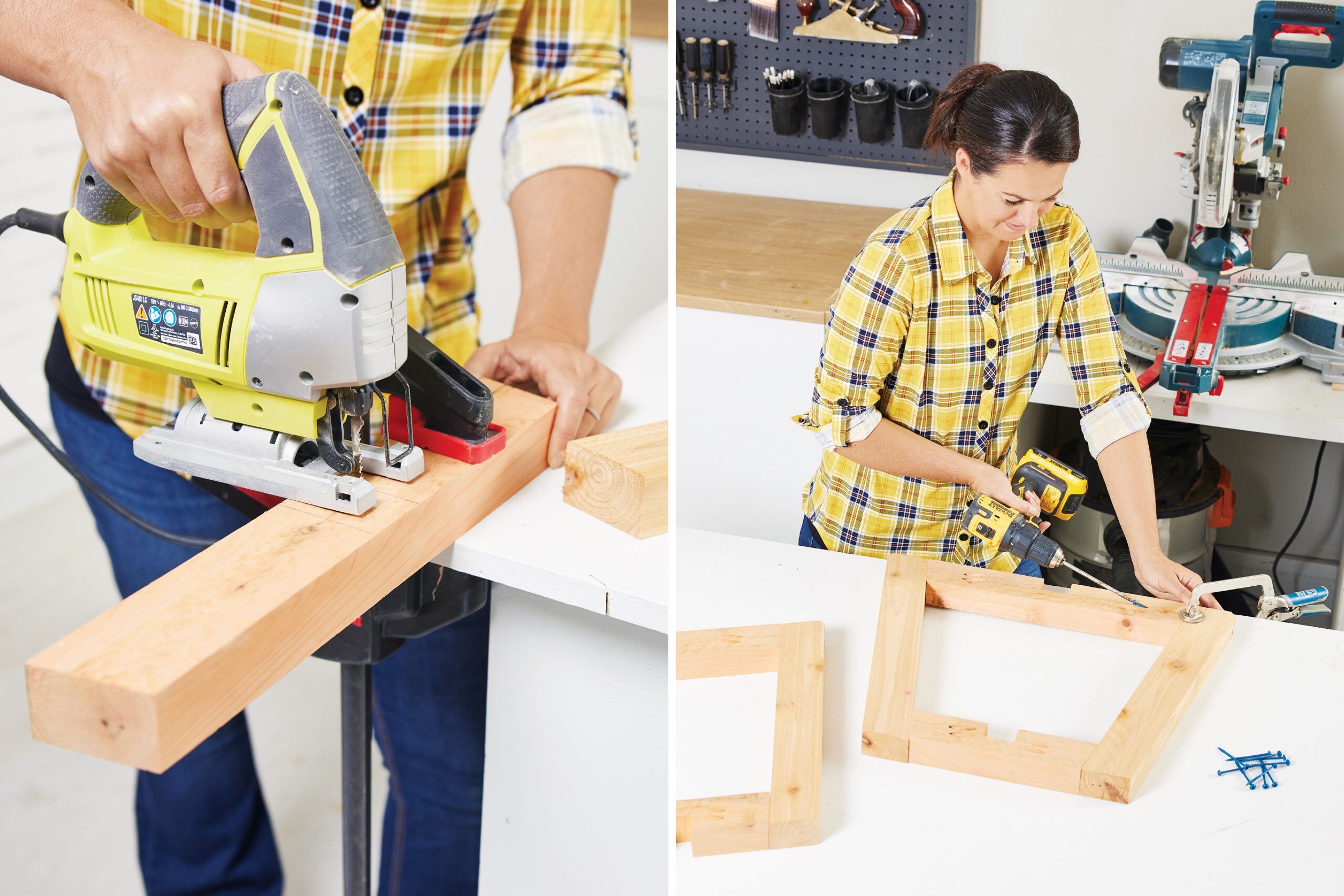
4. Notch the base pieces.
Two legs, one long bottom piece, and one short top piece form each of two interlocking frames that make up the base. On one set, mark a centered 11⁄2-by-11⁄2-inch notch along the top edge of the top and bottom boards; on the other, mark the notches along the bottom edge of the top and bottom boards. Cut out the notches with a jigsaw, periodically dry-fitting the pieces to test the joints.
5. Assemble the frames.
Using a pocket-hole jig and a drill/driver, make holes in the ends of the top and base rails where indicated in the illustration at left. Using pocket screws and glue, completely assemble one frame, but leave the base rail off of the second frame.

6. Interlock the frames.
Fit the frames together as shown; use pocket screws to attach the base rail to the second frame.
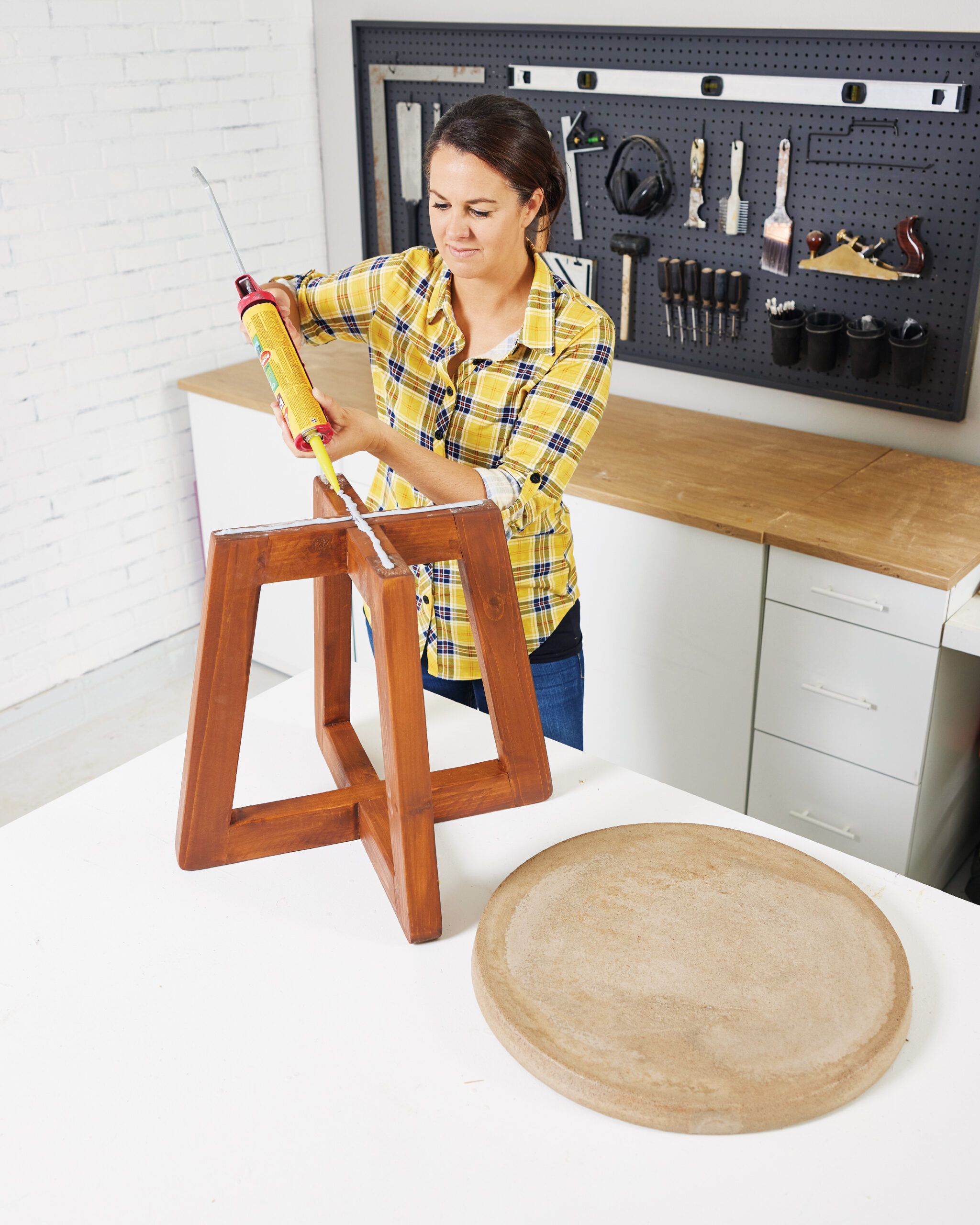
7. Assemble the base.
Apply glue to the notches and press the frames together. Once dry, sand the parts, rounding the clipped corners; apply stain followed by two coats of polyurethane.
8. Attach the top.
Set the top facedown on your work surface. Apply adhesive to the top of the base, then center it on the top. Wait 24 hours before using the table. When the concrete has fully cured, about a month later, seal with wax.
Materials
- 2 – 2×3×8-inch boards
- Concrete countertop mix (80 lbs.)
- 2 – 1⁄2-inch exterior pocket-hole screws
- Wire mesh
- 22-inch metal drip pan
- 5-gallon bucket
- Plastic sheet
- Stain and exterior polyurethane
- Exterior wood glue
- Concrete release agent
- Duct tape
- Adhesive caulk